Effiziente Automatisierung: 16.500 Spritzgussteile in 12 Stunden autonom verpackt
Nach Abschluss der Vorentwicklung und Serienstart mit stabiler Serienproduktion, forderte der Kunde plötzlich die Lieferung der Teile lagerichtig gesetzt in eigenen Verpackungen.
Angesichts einer Ausbringung von rund 1400 Teilen pro Stunde ist diese zusätzliche Aufgabe unmöglich wirtschaftlich in Handarbeit zu bewältigen. Eine standardisierte und zuverlässige Automationslösung mit Roboter und Traystapler erledigt diesen Job jetzt zuverlässig.
- Branchen
- Chemie und Kunststoff
- Anwendungsmöglichkeiten
- Handling
- Kunde
- EGS Automation GmbH
- Produkte
- GP7 - GP-Serie
Die Franz Wolf Kunststoffverarbeitung GmbH ist ein mittelständisches Familienunternehmen in dritter Generation und seit über 50 Jahren am Markt. Ansässig in Kirchheim im Unterallgäu sind dort rund 40 Mitarbeitende beschäftigt. Spricht man mit Petra Kaiser, geschäftsführende Gesellschafterin, und Moritz Kaiser, technischer Geschäftsführer, geben beide neben der langjährigen Kompetenz in der Spritzgießfertigung, den eigenen Werkzeugbau als eine Schlüsselkompetenz für den Erfolg an. Dieser Bereich garantiert hohe Qualität, auch über eine lange Produktionsdauer und hohe Stückzahlen. Er gewährleistet aber auch die notwendige Flexibilität für Prototypentwicklungen und Kleinserien.
Der Maschinenpark von Wolf Kunststoffverarbeitung umfasst rund 40 Maschinen im Schließkraftbereich von 15 bis 130 Tonnen und wird regelmäßig modernisiert. Inzwischen sind rund ein Drittel der Maschinen vollelektrisch, was sich entsprechend positiv auf den Energieverbrauch des Unternehmens auswirkt.
Beliefert werden Kunden aus den Bereichen Automotive, Elektronik, Hydraulik, Sensorik sowie Kommunikation.
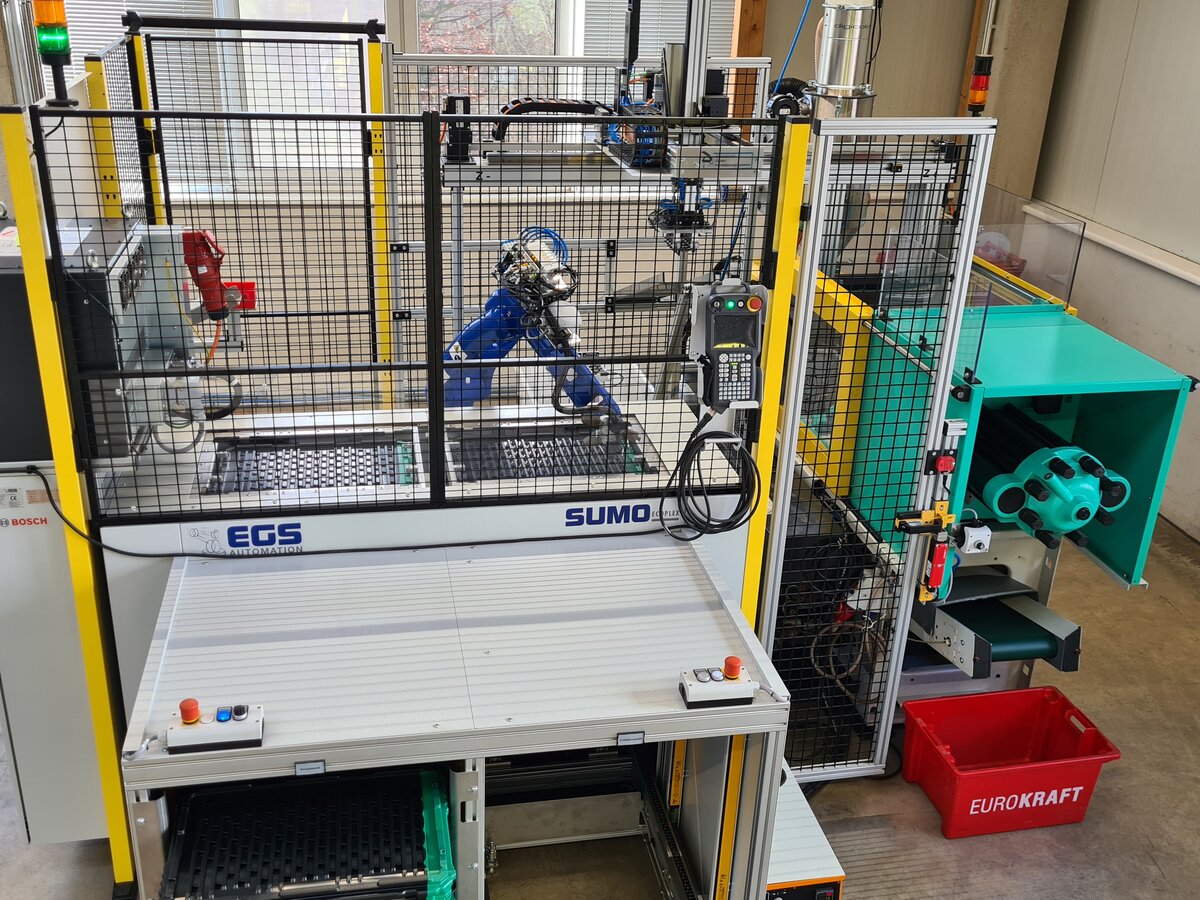
Bild: Gesamtanlage mit Palettiersystem, Roboter und Übergabestation
Auf einer der Produktionsanlagen wird ein kleines Präzisionskunststoffteil für einen Lenkwinkelsensor in großer Stückzahl gefertigt. Das Teil wird auf einer Arburg Allrounder 40-Tonnen-Maschine achtfach mit Anguss gespritzt. Der komplette Schuss wird von einem Linearhandling entnommen und vom Anguss getrennt. Dabei liegt sich je eine Gruppe von vier Teilen spiegelverkehrt am Anguss gegenüber. Die Einzelteile wurden dann bisher vom Handling auf ein Förderband abgelegt, über dass sie unsortiert in einen Karton gelangten. Die Anlage war fertig konzipiert, aufgebaut und in Betrieb genommen, als plötzlich der Kunde die Firma Wolf mit der Anforderung überraschte die Teile künftig einzeln gesetzt in eigenen, bereits vorhandenen, Verpackungen angeliefert zu bekommen.
Der Beweggrund für diesen Wunsch ist in der Regel, dass die nachfolgende Weiterverarbeitung automatisiert wird und damit die Teile automatisierungsgerecht angeliefert werden müssen. Im konkreten Fall bedeutete das: in Kundentrays im Format 600x400 Millimeter muss eine Ausbringung von rund 1400 Teilen pro Stunde lagerichtig einsortiert werden, jeweils 112 Teile in jedes Tray. Die Trays müssen danach gestapelt auf Europaletten gestellt und mit einem Deckel versehen werden. Das hätte einem Personalbedarf von knapp zwei Personen während der gesamten Produktionszeit entsprochen verbunden mit einer sehr stupiden Aufgabe.
Entnahmehandlings sind zwar eine sehr schnelle und günstige Lösung zur Entnahme von Teilen aus einer Spitzgießmaschine aber nicht wirklich geeignet zum vereinzelten Einsetzen von Teilen in Trays. Das vorhandene Linearhandling war damit kein möglicher Lösungsansatz für das Verpacken in die Trays. Weiterhin musste auch noch eine Lösung für das Entstapeln und Aufstapeln der Trays für die Bereitstellung zum Verpackungsprozess gefunden werden.
Im Angesicht dieser Aufgabenstellung erinnerte sich Moritz Kaiser an eine Information, die er in einem Newsletter von einem Kunden seines Unternehmens bekommen hatte. Dieser langjährige Kunde, die Firma Dunkermotoren, den man mit Spritzgussteilen beliefert, hatte vermeldet, dass ein Automatisierungsunternehmen gekauft wurde und jetzt zur Gruppe und damit zum Mutterkonzern AMETEK gehört.
Die EGS Automation aus Donaueschingen ist seit 2021 ein Tochterunternehmen von Dunkermotoren und seit 1999 Anbieter von roboterbasierten Automationssystemen.
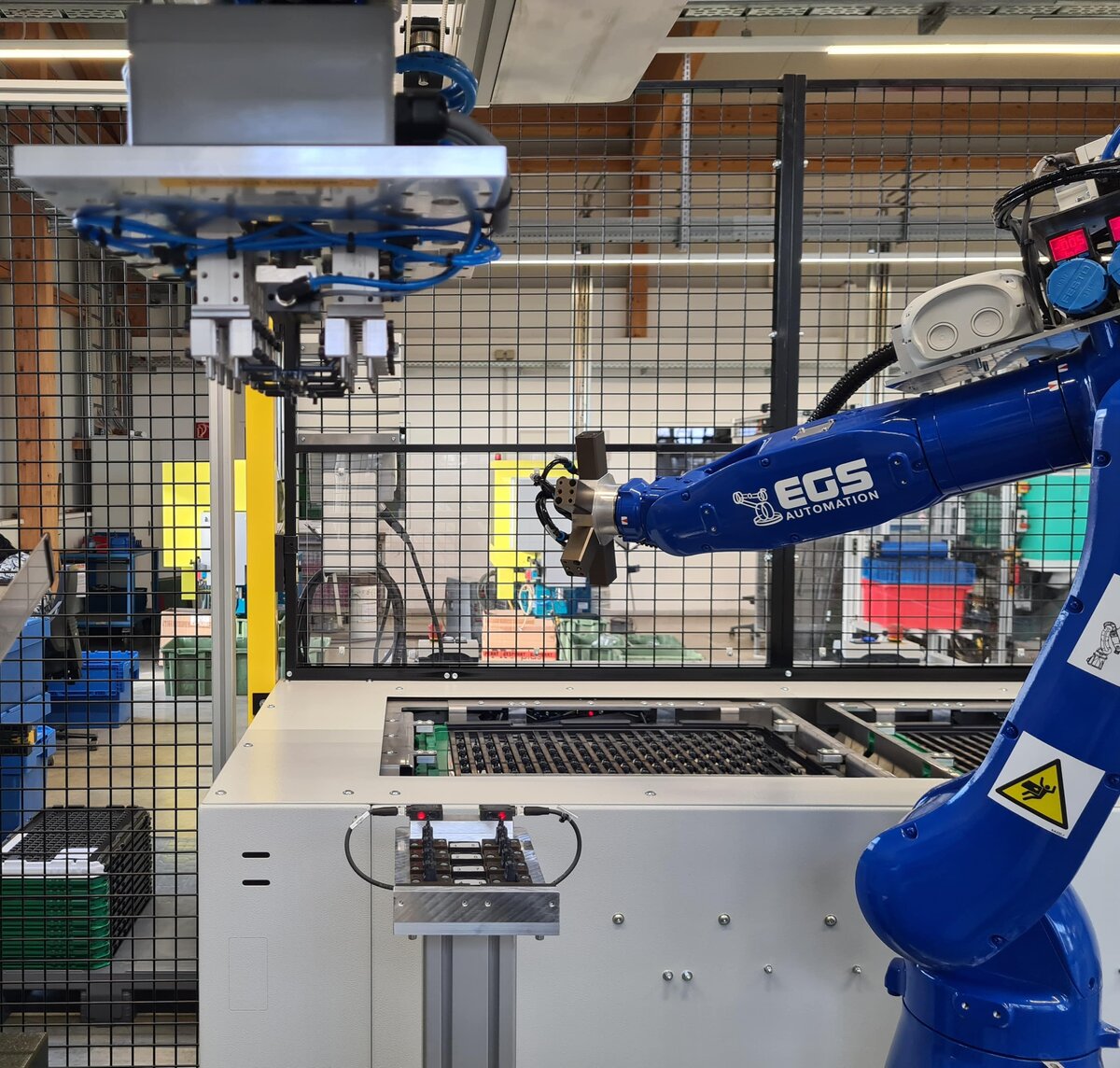
Bild: Teileübergabe vom Entnahmehandling zum Roboter
Mit der Aufgabenstellung konfrontiert, konnte EGS auf Basis eines Standardpalettiersystems die passende Lösung anbieten. Basis der Anlage ist ein SUMO Ecoplex2, ein Traystapler der im Trayformat 600x400 Millimeter Stapel bis zu 0,8 Meter Höhe verarbeiten kann. Diese können über Förderbänder zu- und abgeführt werden. Im konkreten Fall fassen die Bänder vier Stapel, was einer Autonomie von rund 12 Stunden entspricht.
Das Handling der Einzelteile übernimmt dabei ein Knickarmroboter von Yaskawa, ein MOTOMAN GP7 mit knapp einem Meter Reichweite und sieben Kilogramm Traglast.
Blieb noch die Frage nach der Übergabe der Teile aus der SGM. „Das vorhandene Handling von Dürrschmidt sollte weiterhin die Entnahme übernehmen. Es musste also eine Übergabe realisiert werden und wir hatten Sorge, dass es im Bereich der Schnittstelle Probleme sowohl bei der Abstimmung als auch im späteren Betrieb geben könnte.“, äußert Moritz Kaiser seine Bedenken.
„Im konkreten Fall hat es uns die Firma Dürrschmidt mit ihrer kooperativen Haltung bei der Abstimmung sehr einfach gemacht.“, gibt Hartmut Pfalzgraf, bei EGS verantwortlich für dieses Projekt, zu Protokoll.
Technisch wurde die Übergabe so gelöst, dass das Handling den gesamten Schuss ohne Anguss in eine Übergabestation ablegt, in der Anordnung so, wie er im Werkzeug gespritzt wird. In dieser Ablage wird jedes einzelne Teil sensorisch auf Anwesenheit überwacht. Diese Station wurde von EGS entwickelt und ist so ausgelegt, dass sie im Arbeitsbereich beider Roboter platziert ist. Wenn das Handling die acht Teile eines Schusses abgelegt hat, eilt der Yaskawa-Roboter zur Übergabestation, nimmt mit einem Revolvergreifwerkzeug vier Teile nacheinander auf und bewegt sich zum Tray, das im SUMO-Palettiersystem bereits zur Befüllung bereitgestellt ist und legt die vier Teile nacheinander in die nächsten freien Nester. Diesen Vorgang wiederholt er für das zweite Teile-Quartett eines Schusses. Dabei wird auch die gegenüberliegende Orientierung der Teile aus dem Spritzgießwerkzeug aufgelöst und Teil für Teil lagerichtig abgelegt. Die Maschine spritzt alle 21 Sekunden acht Teile, in der Zeit muss also viermal der Weg zwischen Tray und Übergabestation zurückgelegt werden und insgesamt 16 Pick und Place Vorgänge, jeweils mit Umorientierung des Greifwerkzeuges, durchgeführt werden. Eine sportliche Aufgabe, die den Yaskawa-Roboter keine Sekunde stillstehen lässt und seine Dynamik voll ausnutzt.
Die Trays laufen leer im Stapel in den Traystapler ein und werden abgehoben und dem Roboter zum Befüllen bereitgestellt. Nachdem ein Tray gefüllt ist, wird es auf den Stapel mit vollen Trays übergesetzt, so lange bis dieser die volle Höhe erreicht hat und auf dem Förderband ausgefördert wird. Die Bandsysteme am Ein- und Ausgang des Palettiersystems bieten jeweils Platz für vier Stapel mit Leer- und Vier mit gefüllten Trays. Das System kann damit rund 12 Stunden autonom laufen. „Ein Bediener muss lediglich alle 12 Stunden vier gefüllte Stapel vom Band auf eine Europalette umsetzen und diese wegfahren und eine neue leere Europalette holen, sowie vier neue Leertray-Stapel aufsetzen. Alles in Allem weniger als zehn Minuten Arbeit und danach läuft die Automation wieder 12 Stunden autonom.“, freut sich Moritz Kaiser.
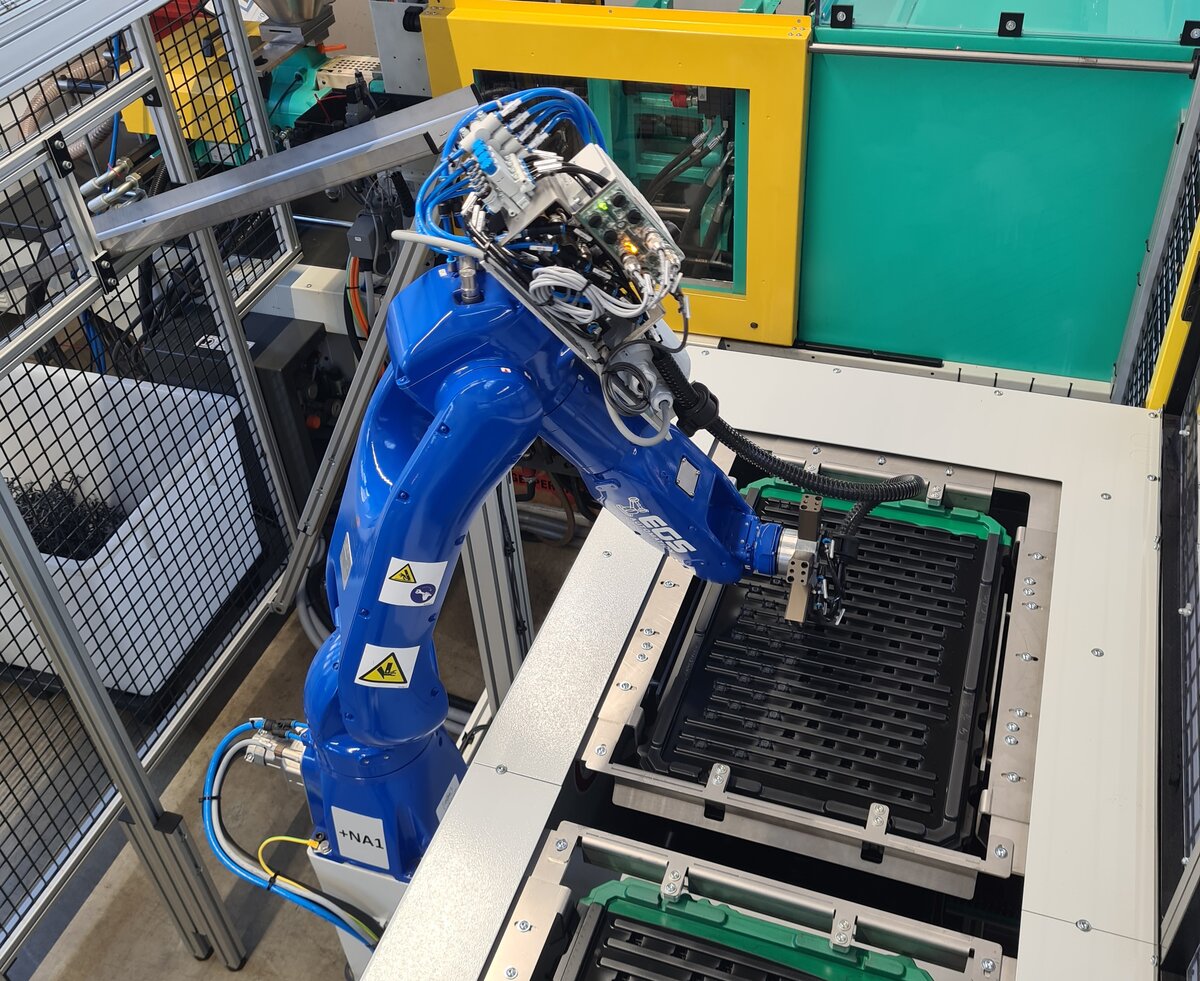
Bild: Der Roboter setzt acht Fertigteile in 21 Sekunden in die Nester der Trays ab
Mit der Anlage hat der erste Knickarmroboter Einzug in die Fertigung der Franz Wolf Kunststoffverarbeitung gehalten. Anfängliche Ängste und Vorbehalte haben sich als unbegründet erwiesen. Mit der Installation und Übergabe der Anlage erfolgte eine zweitägige Einweisung des Bedienpersonals in die Bedienung der Anlage und den Umgang mit möglichen Abbruchsituationen und Problemen.
„Roboterprogrammierkenntnisse sind überhaupt nicht notwendig für die Bedienung der Anlage. Aber wir haben Gefallen an der Robotertechnik mit ihrer Flexibilität und Zuverlässigkeit gefunden. Es wird nicht der letzte Roboter in unserer Fertigung sein und wir wollen uns Schritt für Schritt mehr in das Thema einarbeiten. EGS unterstützt uns dabei genau in dem Maß, wie wir es wollen und brauchen.“, lobt Petra Kaiser die bisherige Zusammenarbeit und gibt Ausblick auf die nähere Zukunft.
„Wir waren darüber hinaus sehr überrascht über die ausführliche und anschauliche Anlagendokumentation und Bedienungsanleitung, die mit der Anlage geliefert wurde. Das ist offenkundig nicht nur Dokumentationsmaterial, um der Einhaltung von Normen und Vorschriften zu genügen, sondern auch anschaulich und für den regelmäßigen Gebrauch gemacht“ sagt Moritz Kaiser zum Abschluss.
Die Automation wurde nachträglich in die vorhandenen räumlichen Gegebenheiten integriert, die Maschine und Aggregate mussten dafür nicht versetzt werden. Das SUMO-System erlaubt die weitgehend freie Ausrichtung des Palettiersystems zum Roboter, so dass die Bedienerseite optimal zur Materiallogistik ausgerichtet werden kann.
Author: Heiko Röhrig; Senior Business Development Manager, EGS Automation GmbH
Fotos: ©EGS Automation